Modern logistics management requires more than inventory control and delivery tracking. More than ever, it depends on the ability to forecast demand, identify bottlenecks in advance, and make data-driven decisions.
In this context, Artificial Intelligence (AI) and Data Science have become strategic allies—not just for automating tasks, but for transforming the way the entire supply chain operates.
In this article, we explore how AI can be used to predict the consumption of parts and supplies—a critical logistics step—and how that impacts other links in the chain, such as warehousing, transportation, and replenishment.
To illustrate this, we present a real case from Venturus, showing how this technology can improve efficiency, reduce waste, and strengthen supply chain intelligence in practice. Let’s dive in!
The Importance of Forecasting in the Supply Chain
Logistics is, by definition, an interconnected system. Any imbalance between supply and demand can trigger a chain reaction: overstocked warehouses, shortages of critical materials during repairs, delayed deliveries, rescheduled routes, and ultimately, dissatisfied customers.
One of the biggest challenges in logistics operations lies in the unpredictability of consumption. When it’s unclear what will be needed, when, and in what quantity, decisions on purchasing, shipping, and inventory are often based on guesswork.
The result? Poorly sized stock levels, increased costs, and higher operational risk.
The good news is that with AI, it’s possible to bring predictability to this process. And when consumption becomes more predictable, the rest of the chain becomes more efficient.
Artificial Intelligence in Logistics: Beyond Automation
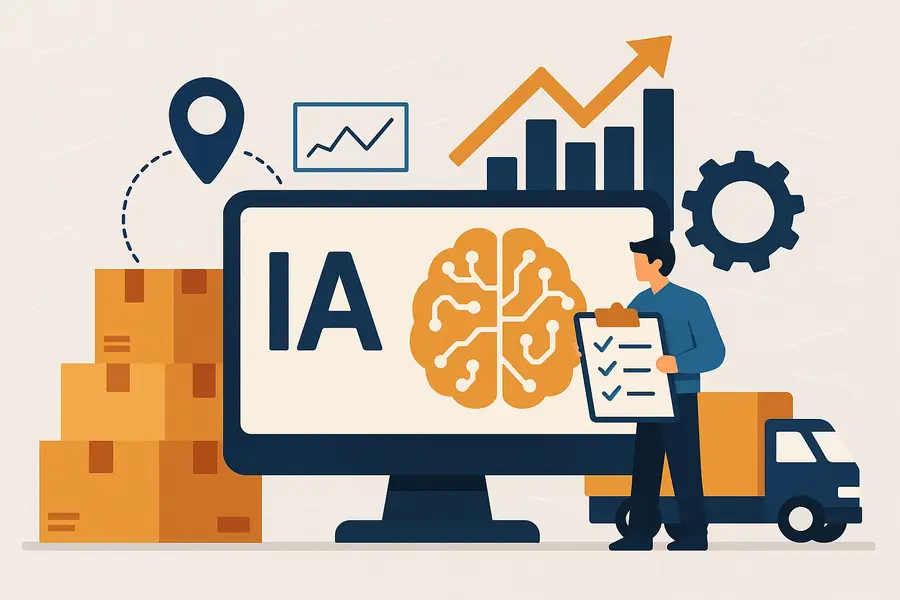
AI, especially through machine learning techniques, enables systems to learn from historical data and predict future behavior.
When applied to logistics, AI acts as a Supply Chain Intelligence tool—connecting different data sources and generating real-time insights.
In the context of parts and supplies, AI can anticipate which items are likely to be needed for each type of service, forecast seasonal demand, identify replacement patterns, and even detect anomalies that may indicate errors, waste, or opportunities for improvement.
These predictions not only optimize resource usage but also influence key decisions such as:
- Purchase planning and restocking
- Inventory sizing across distribution centers
- Route planning for transportation
- Service prioritization based on part availability
The Venturus Case: Smart Predictions in the Repair Process
A practical example of this approach was developed by Venturus in partnership with a global company in the payment technology sector.
The issue lay in high and unpredictable consumption during the repair of payment terminals, leading to inventory shortages, service delays, and increased costs.
The solution involved building an AI model that, based on the defects reported for each device, could predict which parts would likely be required for the repair.
The model was trained using:
Over 1.8 million service orders
225 types of defects
722 types of parts
Using a learning-to-rank and multi-label classification approach, the system generated a ranked list of expected parts for each service. At the end of the process, these predictions were compared with the actual parts used, and discrepancies were flagged for review.
Measurable Impacts on Logistics Operations
The impact was direct and quantifiable:
- 90% accuracy in part consumption predictions in the most recent weeks
- A drop from 10% to 4% in parts consumed outside of model predictions—representing a 60% reduction in incorrect usage
- Improved logistics alerting, enabling real-time restocking and correction
- Better purchase and distribution planning, lowering the risk of stockouts and overstocking
But the results extended beyond the repair process itself. With predictions integrated into a logistics control system, the company was able to:
- Plan restocking of service centers with greater accuracy
- Reduce the number of emergency deliveries
- Improve the efficiency of internal transport between warehouses
- Support prioritization of service calls based on available parts
The model proved scalable, with weekly updates and the ability to adapt to new consumption patterns. More than just a predictive tool, it became a strategic element of the company’s logistics chain.
Discover other successful cases here!
Broadening the Scope: From Parts to Complete Logistics Processes
This repair and parts case is just one example of how AI can be applied in logistics. The same concept can be used to predict the consumption of any type of supply or operational resource, such as:
- Raw materials in manufacturing: anticipate demand by production line and reduce downtime
- Retail products: align store restocking with sales trends and seasonality
- Hospital supplies: ensure availability of critical items based on service history
- Field service: assemble personalized kits for each service call, reducing return visits
In all these cases, AI acts as a driver of operational intelligence—linking consumption data to logistics planning, transportation, inventory, and even workforce training.
AI as a Competitive Edge in Logistics
In a landscape where efficiency and agility are key to success, AI is a crucial tool for turning logistics into a competitive advantage. The predictive power of intelligent models enables faster decisions, less waste, and better resource allocation.
The case presented here offers a clear example of how AI can be applied in a practical, strategic way. More importantly, it shows that this type of solution is adaptable across sectors and challenges.
If your company operates logistics processes and is looking for more control, less waste, and a better customer experience—now is the time to explore how AI can support your goals.
After all, you already have the data. The next step is to use it intelligently. Talk to our experts and discover how!